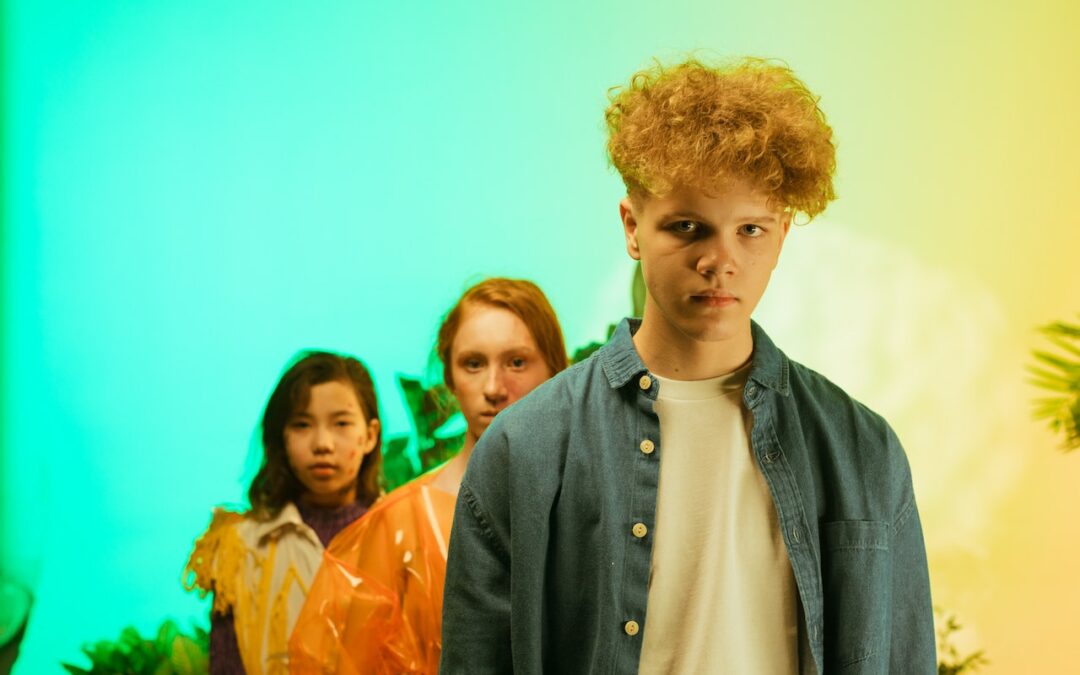
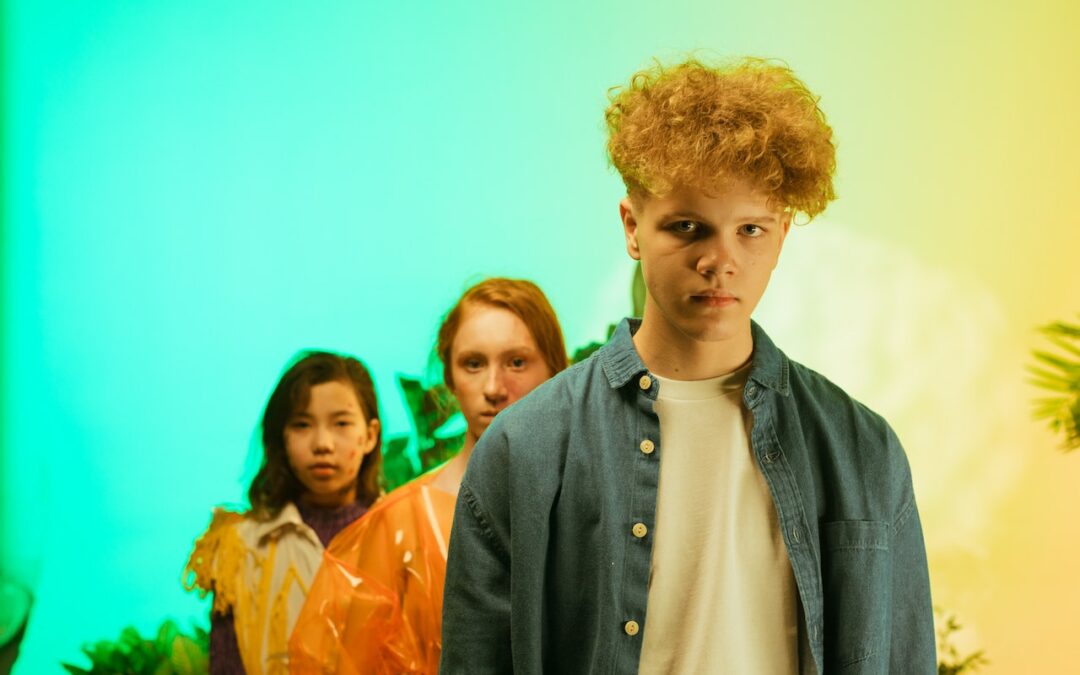
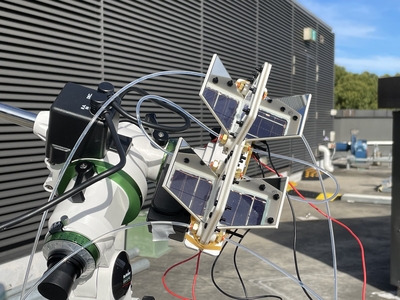
Photosynthesis inspires net-zero ammonia research
Scientists from UNSW Sydney have come up with a novel way to sustainably produce ammonia, inspired by the natural process of photosynthesis. Their research has been published in the Journal of Energy and Environmental Science.
Ammonia is a gas that is essential for producing the fertilisers that support global agriculture and food production. However, traditional methods of making ammonia create significant greenhouse gas emissions, since fossil fuels are required for the hydrogen production and energy that power the process.
“Traditional ammonia production requires high temperatures — around 400–500°C — and high pressure, historically necessitating the use of fossil fuels,” said UNSW Scientia Professor Rose Amal, from the School of Chemical Engineering.
To address this problem, teams led by Amal and Professor Xiaojing Hao, from the School of Photovoltaic and Renewable Energy Engineering, developed a way to generate ammonium ions from nitrate-containing wastewater using only a specially designed solar panel that works like an artificial leaf. Using a process known as photoelectrocatalytics (PEC), the researchers placed on the panel a nanostructured thin layer of copper and cobalt hydroxide that acted as a catalyst for the chemical reaction needed to produce ammonium nitrate from the wastewater.
In a real leaf, photosynthesis is the process by which plants use sunlight, water and carbon dioxide to create oxygen and energy in the form of sugar. This new photoelectrocatalytic process mimics photosynthesis, with the solar panel acting like an artificial leaf, using sunlight and nitrate-containing wastewater to create ammonium nitrate.
Artificial leaf system developed at UNSW to create ammonia from wastewater using only the sun. Image credit: Chen Han/UNSW.
The research team, which includes lead author Chen Han and Dr Jian Pan (a DECRA fellow), built a 40 cm2 artificial leaf system on the roof of Tyree Energy Technologies building at UNSW that has been able to produce ammonium ions that can satisfy 1.49 m2 of cropland.
“We think this new technology could be implemented on a relatively small scale in agricultural locations to produce ammonium onsite, which would decentralise the production process and further reduce CO2 emissions that are associated with the transportation process,” Amal said.
“Our findings provide a clean, efficient and cost-effective solution for utilising solar energy and chemical wastes to produce ammonia and other value-added products,” Han added.
“You do not need a high concentration of ammonia in fertiliser, so we believe the amounts of ammonia we are producing using our system make it a viable application in the real world, although we definitely still have some ways to further improve it.”
The researchers hope that the generation of the ammonium from the wastewater will allow the processed water to be used to irrigate crops and further help them to grow.
“It’s important to acknowledge that the wastewater we convert isn’t coming directly from municipal waste or runoff — it still needs to be processed first to filter out the organic matters and particulates,” Amal said.
“But we are hopeful that once we have generated ammonium from the nitrate wastewater, the treated water can then be put into irrigation.”
Amal is keen for further collaboration and involvement with potential industry partners to develop the process into a fully viable commercial system.
“Industry partners would help us scale up this device, and we definitely would like to utilise a full-scale, traditionally sized solar panel for our application,” she said.
“This is important for helping us reach our emissions targets of 2030 and 2040, and ultimately achieving net zero by 2050. We want to produce ammonia in a cleaner and greener way that minimises CO2 emissions.”
Top image caption: The photoelectrode utilising nanostructured thin layer of copper and cobalt hydroxide helps to create ammonia from wastewater using only the sun. Image credit: Chen Han/UNSW.
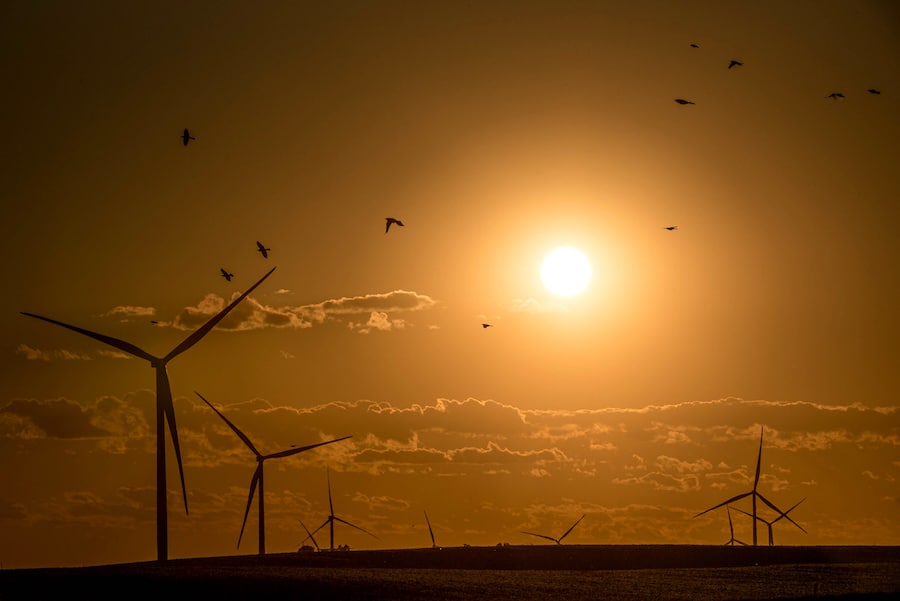
Australia Could Prevent Thousands of Bats From Being Killed Each Year by Wind Turbines With Simple Fix, Study Finds
Wind farm operators in Australia are being encouraged to use the simple method of curtailment — increasing the wind speed required for turbines to start rotating — which a new study has found can drastically lower how many bats are killed by the enormous blades. The tactic is already being used in the United States, […]
The post Australia Could Prevent Thousands of Bats From Being Killed Each Year by Wind Turbines With Simple Fix, Study Finds appeared first on EcoWatch.
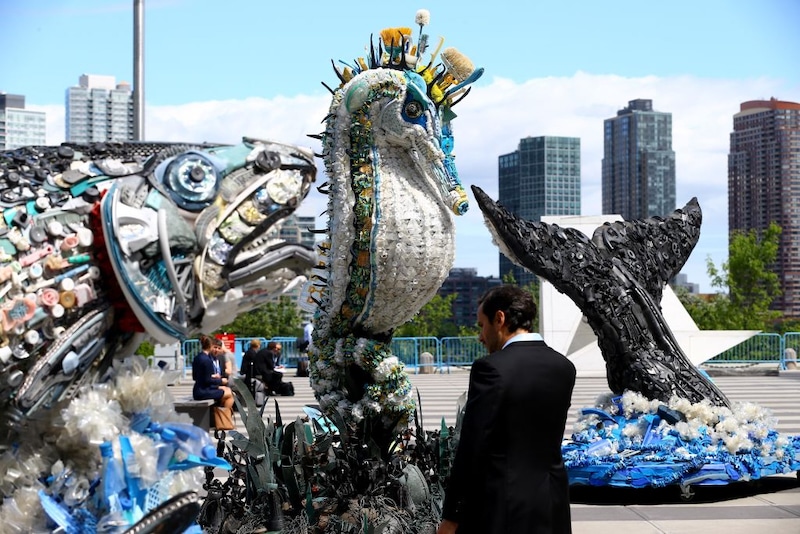
U.S. Signals New Support for Global Plastics Reduction, Reports Say
The U.S. has shifted its policy position and is now in favor of supporting limitations on global plastics, Reuters confirmed. As reported by Grist, the Biden administration announced in closed-door meetings this week that it supported global efforts to limit plastic pollution via the United Nations’ plastic treaty. Previously, the U.S. had held the stance […]
The post U.S. Signals New Support for Global Plastics Reduction, Reports Say appeared first on EcoWatch.
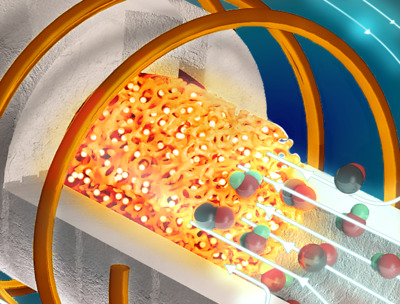
Decarbonising the industrial process sector
Researchers at Stanford Engineering have designed and demonstrated a new type of thermochemical reactor that is capable of generating the immense heat required for many industrial processes with fewer carbon emissions. The electrified design, published in Joule, is also claimed to be smaller, cheaper and more efficient than existing fossil fuel technology.
“We have an electrified and scalable reactor infrastructure for thermochemical processes that features ideal heating and heat-transfer properties,” said Jonathan Fan, an associate professor of electrical engineering at Stanford and senior author on the paper. “Essentially, we’re pushing reactor performance to its physical limits, and we’re using green electricity to power it.”
Magnetic way to heat
Most standard thermochemical reactors work by burning fossil fuels to heat a fluid, which then flows into pipes in the reactor — like a boiler sending hot water to cast iron radiators in an old house, but with better insulation and at much higher temperatures. This requires a large amount of infrastructure and there are many opportunities to lose heat along the way.
The electrified reactor uses magnetic induction to generate heat — the same sort of process used in induction stoves. Instead of having to transport heat through pipes, induction heating creates heat internally within the reactor, by taking advantage of interactions between electric currents and magnetic fields. If you wanted to inductively heat up a steel rod, for example, you could wrap a wire around it and run an alternating current through the coil. These currents create an oscillating magnetic field which, in turn, induces a current in the steel. And because steel is not a perfect conductor of electricity, some of that current turns into heat. This method effectively heats the whole piece of steel at the same time, rather than creating heat from the outside in.
This image depicts the inductively heated metamaterial reactor with catalysts filling the ceramic foam baffle. It is producing carbon monoxide and water from the reverse water gas shift reaction. Image credit: Dolly Mantle.
Adapting induction heating for the chemicals industry is not as easy as just turning up the heat. Industrial reactors need to evenly create and distribute heat in a three-dimensional space and be much more efficient than the average stovetop. The researchers determined that they could maximise their efficiency by using particularly high frequency currents, which alternate very quickly, in conjunction with reactor materials that are particularly bad conductors of electricity.
The researchers used new, high-efficiency electronics developed by Juan Rivas-Davila, an associate professor of electrical engineering and co-author on the paper, to produce the currents they required. They then used those currents to inductively heat a three-dimensional lattice made of a poorly conducting ceramic material in the core of their reactor. The lattice structure is just as important as the material itself, Fan said, because the lattice voids artificially lower the electrical conductivity even further. And those voids can be filled with catalysts — the materials that need to be heated to initiate chemical reactions. This makes for even more efficient heat transfer and means the electrified reactor can be much smaller than traditional fossil fuel reactors.
“You’re heating a large surface area structure that is right next to the catalyst, so the heat you’re generating gets to the catalyst very quickly to drive the chemical reactions,” Fan said. “Plus, it’s simplifying everything. You’re not transferring heat from somewhere else and losing some along the way, you don’t have any pipes going in and out of the reactor — you can fully insulate it. This is ideal from an energy management and cost point of view.”
Capturing industrial applications
The researchers used the reactor to power a chemical reaction, called the reverse water gas shift reaction, using a new sustainable catalyst developed by Matthew Kanan, a professor of chemistry in the School of Humanities and Sciences and co-author of the paper. The reaction, which requires high heat, can turn captured carbon dioxide into a valuable gas that can be used to create sustainable fuels. In the proof-of-concept demonstration, the reactor was over 85% efficient, indicating that it converted almost all electrical energy into usable heat. The reactor also demonstrated ideal conditions for facilitating the chemical reaction — carbon dioxide was converted to usable gas at the theoretically predicted rate, which is often not the case with new reactor designs.
“As we make these reactors even larger or operate them at even higher temperatures, they just get more efficient,” Fan said. “That’s the story of electrification — we’re not just trying to replace what we have, we’re creating even better performance.”
Fan, Rivas-Davila, Kanan and their colleagues are already working to scale up their new reactor technology and expand its potential applications. They are adapting the same ideas to design reactors for capturing carbon dioxide and for manufacturing cement, and they are working with industrial partners in the oil and gas industries to understand what those companies would need to adopt this technology. They are also conducting economic analyses to understand what system-wide sustainable solutions would look like and how they could be made more affordable.
“Electrification affords us the opportunity to reinvent infrastructure, breaking through existing bottlenecks and shrinking and simplifying these types of reactors, in addition to decarbonising them,” Fan said. “Industrial decarbonisation is going to require new, systems-level approaches, and I think we’re just getting started.”
Image credit: iStock.com/tommy