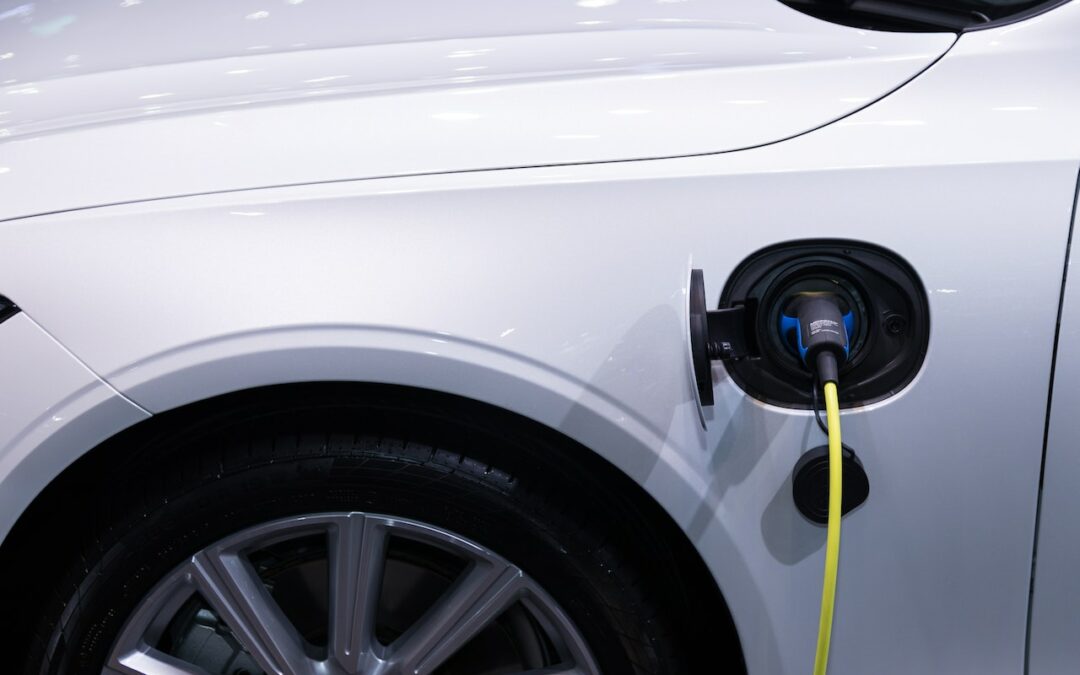
Mystery electric coupe spied: BMW Neue Klasse sports car or something else?
An outlandish prototype of a compact electric coupe has been spotted with BMW-like design elements
An outlandish prototype of a compact electric coupe has been spotted with BMW-like design elements
A herd of elephants has arrived in Newport, Rhode Island, on the first leg of their 3,500-mile journey across the U.S. Jointly organized by two nonprofits, Elephant Family and CoExistence, the monumental public work draws attention to the relationships between people and wildlife, particularly as the human population grows and encroaches on natural habitats.
“The Great Elephant Migration” features 100 life-sized animal sculptures crafted by the CoExistence Collective, an organization of 200 Indigenous artisans from the Bettakurumba, Paniya, Kattunayakan, and Soliga communities. More
Do stories and artists like this matter to you? Become a Colossal Member today and support independent arts publishing for as little as $5 per month. The article 100 Life-Sized Elephants Lumber Along a Newport Cliff in a Global Conservation Project appeared first on Colossal.
Google’s goal of lowering its carbon footprint is in trouble as the technology company’s energy consumption has increased due to the amount of power needed for artificial intelligence (AI) data centers. According to the internet giant’s annual environmental report, its greenhouse gas emissions have increased by 13 percent in the past year, due mostly to […]
The post AI Energy Demand Drives Google’s Emissions Up 48% in Five Years appeared first on EcoWatch.
Welcome to the future of energy management with the Power Sonic Pulse. Featuring an inverter, solar controller, and high-performance battery packs, the Pulse sets a new standard for efficiency and sustainability. Imagine effortlessly capturing, storing, and optimizing energy on-site. Whether connected to solar panels, renewable sources, or operating independently, the Pulse ensures a reliable energy … Continued
MINI’s truly hot electric Cooper will be previewed at this year’s Goodwood Festival of Speed