This post was originally published on Power Sonic
The electric vehicle (EV) revolution is driving rapid growth in charging infrastructure, posing new challenges for grid capacity, deployment speed, and cost. Battery-buffered EV charging systems offer a breakthrough solution to these challenges, expanding efficient, cost-effective charging infrastructure without overburdening the electric grid. This technology is changing how cities, businesses, and fleet operators build and manage EV charging networks, paving the way for widespread electric vehicle adoption.
What is Battery-Buffered EV Charging?
Battery-buffered EV charging utilizes energy storage to bridge the gap between grid limitations and charging demands. These systems can either be all-in-one charging systems with fully integrated batteries or can include separate battery energy storage systems working in combination with EV charging stations. These systems store power from the grid during low-demand periods and release it during peak charging times. They maintain a steady draw from the grid while delivering high-power charging to vehicles. Unlike traditional EV charging stations that pull their full load from the grid all at once, battery-buffered systems separate grid power needs from vehicle charging demands, allowing high-power charging even in areas with limited grid capacity.
Key Financial Benefits: Significant Cost Savings
Battery-buffered electric vehicle charging offers compelling cost advantages by reducing the need for costly grid upgrades. Traditional charging infrastructure often requires significant investments in substations and power distribution equipment. Still, battery-buffered systems reduce or eliminate these needs.
For example, a project evaluated by NREL for the DOT for four 150 kW DC fast charging stations estimated that project costs, including a small substation, would be $4 million. However, utilizing energy storage instead would reduce project costs to around $1.2-$1.5 million, a 65% savings. Beyond initial capital savings, these systems reduce operational energy costs through demand charge management.
The below table shows the estimated project cost comparison from NREL.
Line Item | Substation Upgrade Approach | Battery-Buffered EV Charging Approach |
DC Fast Charging Stations | $1,000,000 | $1,000,000 |
Battery Energy Storage System | – | $200,000 – $500,000 |
Substation (small) | $3,000,000 | – |
Total Project Cost* | $4,000,000 | $1,200,000 – $1,500,000 |
Timeline | 3-6 years | 1-2 years |
By charging batteries during off-peak times when rates are lower, operators can avoid high-demand fees, which often make up a large part of operational expenses. In some markets, battery-buffered stations can earn additional revenue by participating in demand-side response programs, opening new income streams that traditional EV charging stations cannot access.
Enhanced Operational Efficiency: Smarter Power Management
Battery-buffered systems revolutionize day-to-day charging operations by optimizing power management. They can dynamically allocate power to multiple charging ports based on demand, ensuring efficient energy distribution. This real-time allocation enables charging stations to serve more vehicles simultaneously while maintaining charging speeds.
Battery-buffered systems also make it easier to incorporate renewable energy sources. Solar or wind energy can be stored in batteries during high production periods and used for vehicle charging when renewable production is low. This approach reduces reliance on grid electricity, making operations more sustainable and economical.
Accelerated Deployment: Faster Infrastructure Expansion
One of the standout advantages of battery-buffered charging is its rapid deployment capability. Unlike traditional charging infrastructure, which can take 3–6 years to deploy due to utility upgrades and permitting processes, battery-buffered systems can be installed in as little as 1–2 years. This shortened timeline allows organizations to respond quickly to growing EV demand without waiting for major grid improvements.
Battery-buffered systems also simplify regulatory approvals, as they place less strain on the grid. This streamlined process can save months or even years, allowing charging infrastructure to be rolled out rapidly, especially in high-priority areas with limited grid capacity.
Flexibility and Scalability: Adapting to Demand
Battery-buffered systems offer unmatched flexibility in scaling and placement. Their modular design allows organizations to start with a few charging ports and expand as demand grows without major grid upgrades. This phased approach keeps infrastructure costs manageable, especially in areas where EV adoption may be more gradual.
Battery-buffered systems also open up new locations for charging stations, including remote or urban areas with limited grid access. This location flexibility expands options for charging station placement, supporting a broader and more accessible charging network.
Minimizing Grid Upgrades: Protecting Infrastructure
According to an analysis by NREL, battery-buffered EV charging systems reduce the need for grid upgrades by 50-80%, providing high-power charging without placing excessive strain on the electrical infrastructure. By smoothing out demand spikes, these systems help protect critical grid components, such as substation transformers, which can cost millions to replace. With battery-buffered systems, peak loads on transformers are reduced, extending their life and potentially avoiding costly upgrades.
Battery-buffered systems also reduce the stress on distribution feeders and service transformers, which can wear down quickly under high loads. By spreading charging loads, these systems minimize thermal stress on components, reducing the frequency and cost of equipment replacements. They also maintain stable voltage levels, reducing the need for voltage regulation equipment.
Real-World Impact: Demonstrated Successes
Battery-buffered EV charging systems are already proving their value across diverse applications. Urban areas with limited grid capacity have successfully deployed high-power chargers without requiring extensive grid upgrades. For example, EVESCO has worked with a major fleet operator who avoided utility upgrade costs by implementing battery-buffered systems at their depot, resulting in significant operational cost savings.
On highways, battery-buffered systems have enabled fast, cost-effective deployment of charging stations, promoting long-distance EV travel. In remote areas, these systems allow charging without major infrastructure investments, making EV charging accessible in otherwise challenging locations.
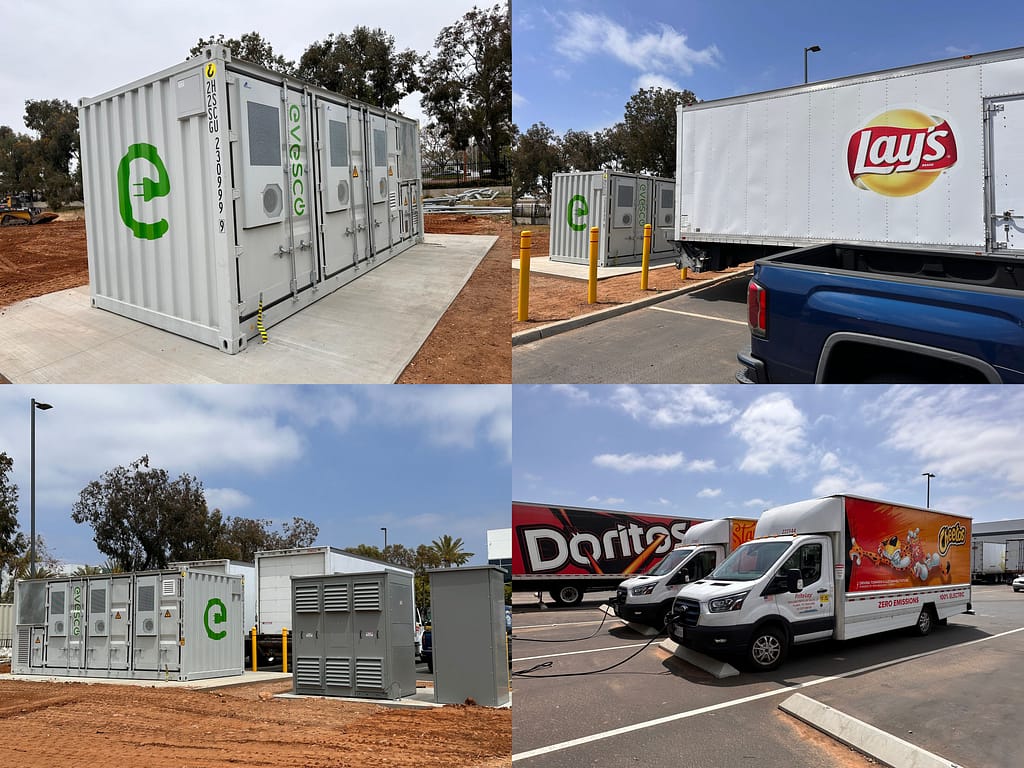
Battery-buffered EV charging is revolutionizing the development of EV infrastructure, offering significant cost, efficiency, flexibility, and speed advantages. For organizations planning to invest in EV charging, these systems present a future-proof solution that combines economic and operational benefits with a reduced impact on the grid. As EV adoption accelerates, battery-buffered systems will support the transition to fleet electrification, enabling organizations to expand charging networks efficiently and sustainably. From lower capital costs and more intelligent power management to faster deployment and grid protection, battery-buffered systems provide a robust foundation for the next generation of EV infrastructure.
0 Comments